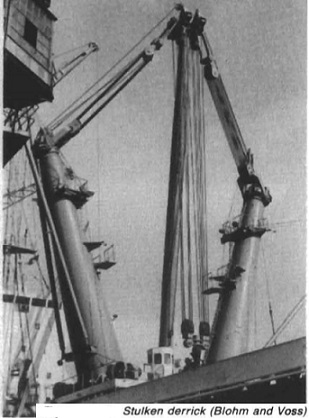
Figure 2: Stulken derrick (Blohm and Voss)
Generally, deck cranes of this type use the "Toplis' three-part reeving system
for the hoist rope and the luffing ropes are rove between the jib head and the
superstructure apex which gives them an approximately constant load,
irrespective of the jib radius. This load depends only on the weight of the jib,
the resultant of loads in the hoisting rope due to the load on the hook passes
through the jib to the jib foot pin (Figure 3 a). If the crane is inclined 5° in
the forward direction due to heel of the ship the level luffing geometry is
disturbed and the hook load produces a considerable moment on the jib which
increases the pull on the luffing rope (Figure 3 b).
In the case of a 55 tonne
crane the pull under these conditions is approximately doubled and the luffing
ropes need to be over-proportioned to meet the required factor of safety. If the
inclination is in the inward direction and the jib is near minimum radius, there is
a danger that its weight moment will not be sufficient to prevent it from luffing
up under the action of the hoisting rope resultant. Swinging of the hook will
produce similar effects to inclination of the crane.
In the Stothert & Pitt 'Stevedore' electro-hydraulic crane the jib is luffed by
one or two hydraulic rams. Pilot operated leak valves in the rams ensure that
the jib is supported in the event of hydraulic pressure being lost and an
automatic limiting device is incorporated which ensures that maximum radius
cannot be exceeded. When the jib is to be stowed the operator can override the
limiting device. In the horizontal stowed position the cylinder rods are fully
retracted into the rams where they are protected from the weather.
Some cranes are mounted in pairs on a common platform which can be
rotated through 360 deg. The cranes can be operated independently or locked
together and operated as a twin-jib crane of double capacity, usually to give
capacities of up to 50 tonnes.
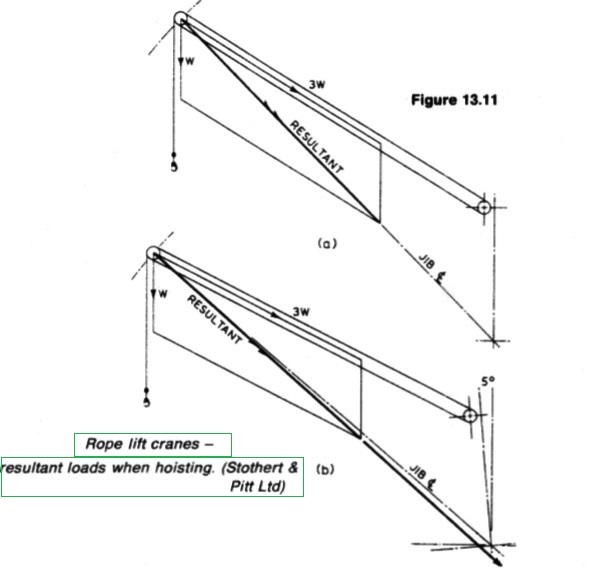
Figure 3: Rope lift cranes - resultant loads when hoisting. (Stothert &
Pitt Ltd)
Most cranes can, if required, be fitted with a two-gear selection to give a
choice of a faster maximum hoisting speed on less than half load. For a 5 tonne
crane full load maximum hoisting speeds in the range 50-75 m/min are
available with slewing speeds in the range 1—2 rev/min. For a 25 tonne
capacity crane, maximum full load hoisting speeds in the range 20—25 m/min
are common with slewing speeds again in the range 1—2 rev/min. On half loads
hoisting speeds increase by two to three times.
Drive mechanism and safety features
In both electric and electro-hydraulic cranes it is usual to find that the crane
revolves on roller bearings. A toothed rack is formed on the periphery of the
supporting seat and a motor-driven pinion meshes with the rack to provide
drive. Spring-loaded disc or band brakes are fitted on all the drive motors.
These are arranged to fail safe in the event of a power or hydraulic failure. The
brakes are also arranged to operate in conjunction with motor cut-outs when
the crane has reached its hoisting and luffing limits, or if slack turns occur on the
hoist barrel.
In the case of the electro-hydraulic cranes it is normal for one electric motor
to drive all three hydraulic pumps and in Ward-Leonard electric crane systems
the Ward-Leonard generator usually supplies all three drive motors.
Summarized below some of the basic operation of deck machinery and maintenance guide :
- Powering deck machinery -Systems and components
Pump and motor systems are used for powering deck machinery such as
winches and windlasses. Pump and actuating cylinders are normally employed
for hatch covers. One or more pumps will be used to supply the volume of fluid
at the pressure required to operate one or more motors.
......
- Mooring equipment for general cargo vessel
The operation of mooring a vessel has traditionally required the attendance of
a large number of deck crew fore and aft. Supervision of the moorings was also
necessary to maintain correct tension through changes due to the tides and the
loading or unloading of cargo.
......
- Hydraulic systems for deck machinery and cargo equipment
The three essential components for a hydraulic circuit, are the hydraulic fluid
held in a reservoir tank, a pump to force the liquid through the system and a
motor or cylinder actuator to convert the energy of the moving liquid into a
working rotary or linear mechanical force. Valves to control liquid flow and
pressure are required by some systems.
......
- General cargo ship deck machinery electric drives
Electric motors on vulnerable deck areas may be protected against ingress of
water by being totally enclosed in a watertight casing. Vents are provided on
some winches, which must be opened when the motor is operating in port.
......
- Handling deck machinery- Anchor windlasses,Anchor capstan & mooring winches
The windlass cablelifter brakes must be able to control the running anchor
and cable when the cablelifter is disconnected from the gearing when
letting go'. Average cable speeds vary between 5 and 7 m/s during this
operation.
......
- General cargo ship deck deck crane
A large number of ships are fitted with deck cranes. These require less time to
prepare for working cargo than derricks and have the advantage of being able
to accurately place (or spot) cargo in the hold. On container ships using ports
without special container handling facilities, cranes with special container
handling gear are essential.
......
- Mechanically operated steel hatch covers
Hatch cover equipment like the other deck machinery, has to exist in a very
hostile environment and the importance of regular maintenance cannot be
over-emphasized. Drive boxes and electrical enclosures should be checked
regularly for water-tightness.
......
- Derricks and cargo winches -Ship cargo handling gears
The duty of a deck winch is to lift and lower a load by means of a fixed rope on
a barrel, or by means of whipping the load on the warp ends, to top or luff the
derricks, and to warp the ship.
......
Home page||
Cooling ||
Machinery||
Services ||
Valves ||
Pumps ||
Auxiliary Power ||
Propeller shaft ||
Steering gears ||
Ship stabilizers||
Refrigeration||
Air conditioning ||
Deck machinery||
Fire protection||
Ship design
||
Home ||
General Cargo Ship.com provide information on cargo ships various machinery systems -handling procedures, on board safety measures and some basic knowledge of cargo ships that might be useful for people working on board and those who working in the terminal. For any remarks please
Contact us
Copyright © 2010-2016 General Cargo Ship.com All rights reserved.
Terms and conditions of use
Read our privacy policy|| Home page||