Home page||Deck machinery||
Handling deck machinery- Anchor windlasses,Anchor capstan & mooring winches
Anchor handling:
The efficient working of the anchor windlass is essential to the safety of the
ship. An anchor windlass can expect to fulfil the following:
1. The windlass cablelifter brakes must be able to control the running anchor
and cable when the cablelifter is disconnected from the gearing when
letting go'. Average cable speeds vary between 5 and 7 m/s during this
operation.
2. The windlass must be able to heave a certain weight of cable at a specified
speed. This full load duty of the windlass varies and may be as high as
70 tonne; figures between 20 and 40 tonne are not unusual. Commonly the
load is between 4 and 6 times the weight of one anchor. The speed of haul
is at least 9m/min and up to 15 m/min.
3. The braking effort obtained at the cable lifter must be at least equal to 40%
of the breaking strength of the cable.
Most anchor handling equipment incorporates warpends for mooring
purposes and light line speeds of up to 0.75 to 1.0 m/s are required. The
conventional types of equipment in use are as follows.
Mooring windlasses
This equipment is self contained and normally one electric or hydraulic motor
drives two cablelifters and two warpends. The latter may not be declutchable
and so will rotate when the cablelifters are engaged. There is some variation
in the detailed design of cablelifters and in their drives. Figure 13.4 shows a
typical arrangement.
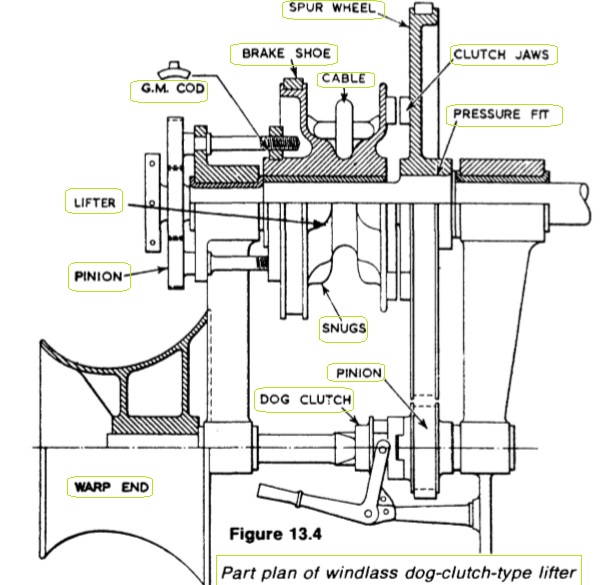
Figure : Part plan of windlass dog clutch type lifter
Due to the low speed of rotation required of the
cablelifter whilst heaving anchor (3—5 rev/min) a high gear reduction is
needed when the windlass is driven by a high-speed electric or hydraulic
motor. This is generally obtained by using a high ratio worm gear followed
by a single step of spur gears between the warpend shaft and cablelifters,
typically as shown in Figure 13.5. Alternatively, multi-steps of spur gear are
used.
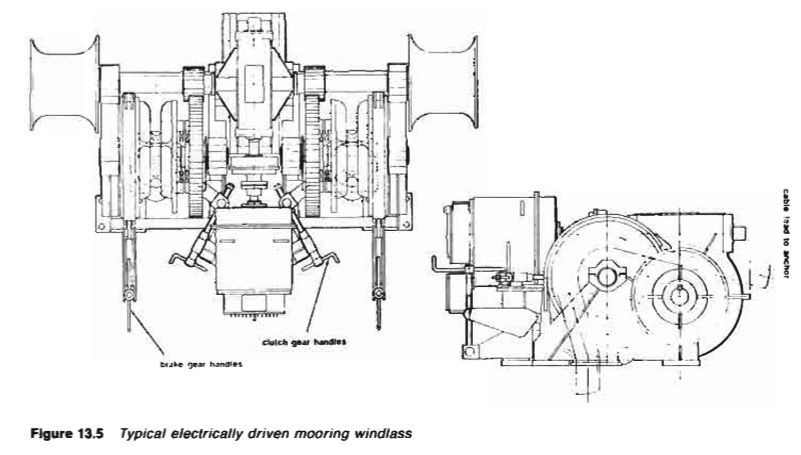
Figure : Typical electrically driven mooring windlass
Anchor capstans
With this type of equipment the driving machinery is situated below the deck
and the cablelifters are mounted horizontally, being driven by vertical shafts as
shown in Figure 13.6. In this example a capstan barrel is shown mounted above
the cablelifter (not shown) although with larger equipment (above 76 mm dia.
cable) it is usual to have only the cablelifter, the capstan barrel being mounted
on a separate shaft.
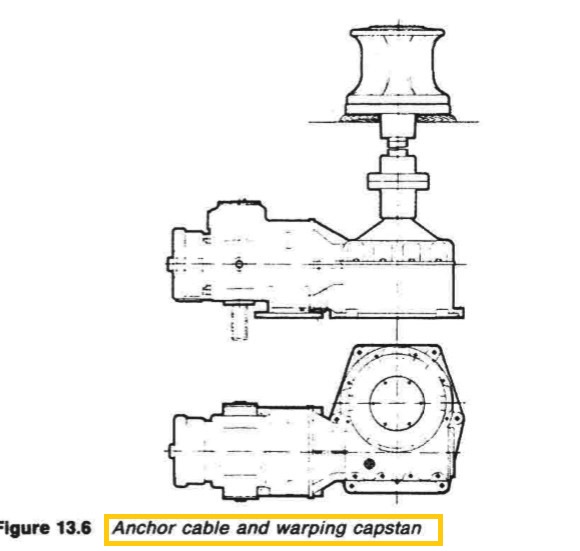
Figure : Anchor cable and warping capstan
Winch windlasses
This arrangement utilizes a forward mooring winch to drive a windlass unit
thus reducing the number of prime movers required. The port and starboard
units are normally interconnected, both mechanically and for power, in order
to provide a stand-by drive and to utilize the power of both winches on the
windlass should this be required.
Control of windlasses
As windlasses are required for intermittent duty only, gearing is designed with
an adequate margin on strength rather than on wear.
Slipping clutches (Figure 13.7) may be fitted between the drive motors and
the gearing to avoid the transmission of inertia in the event of shock loading on
the cable when, for example, the anchor is being housed.
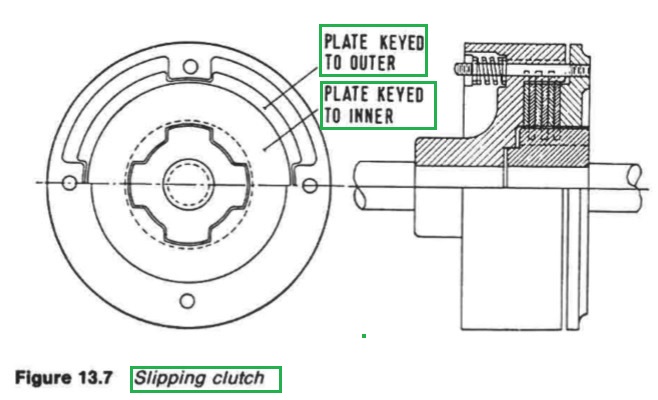
Figure : Slipping clutch
Windlasses are normally controlled from a local position, the operator
manually applying the cablelifter brake as required to control the speed of the
running cable, and whilst heaving anchor the operator is positioned at the
windlass or at the shipside so that he can see the anchor for housing purposes.
It is quite feasible, however, to control all the functions of the windlass from a
remote position. The spring applied cablelifter brakes are hydraulically
released, and to aid the operator the running cable speed and the length paid
out are indicated at the remote position during letting go. The cablelifter can
also be engaged from the remote position so that the anchor can be veered out
to the waterline before letting go or heaved in as required.
The windlass is in the most vulnerable position so far as exposure to the
elements is concerned and maintenance demands should be an absolute
minimum. Normally primary gearing is enclosed and splash lubricated,
maintenance being limited to pressure grease points for gunmetal sleeve
bearings. However, due to the large size of the final of the bevel or spur
reduction gears, and the clutching arrangements required, these gears are often
of the open type and are lubricated with open gear compounds.
Summarized below some of the basic operation of deck machinery and maintenance guide :
- Powering deck machinery -Systems and components
Pump and motor systems are used for powering deck machinery such as
winches and windlasses. Pump and actuating cylinders are normally employed
for hatch covers. One or more pumps will be used to supply the volume of fluid
at the pressure required to operate one or more motors.
......
- Mooring equipment for general cargo vessel
The operation of mooring a vessel has traditionally required the attendance of
a large number of deck crew fore and aft. Supervision of the moorings was also
necessary to maintain correct tension through changes due to the tides and the
loading or unloading of cargo.
......
- Hydraulic systems for deck machinery and cargo equipment
The three essential components for a hydraulic circuit, are the hydraulic fluid
held in a reservoir tank, a pump to force the liquid through the system and a
motor or cylinder actuator to convert the energy of the moving liquid into a
working rotary or linear mechanical force. Valves to control liquid flow and
pressure are required by some systems.
......
- General cargo ship deck machinery electric drives
Electric motors on vulnerable deck areas may be protected against ingress of
water by being totally enclosed in a watertight casing. Vents are provided on
some winches, which must be opened when the motor is operating in port.
......
- Handling deck machinery- Anchor windlasses,Anchor capstan & mooring winches
The windlass cablelifter brakes must be able to control the running anchor
and cable when the cablelifter is disconnected from the gearing when
letting go'. Average cable speeds vary between 5 and 7 m/s during this
operation.
......
- General cargo ship deck deck crane
A large number of ships are fitted with deck cranes. These require less time to
prepare for working cargo than derricks and have the advantage of being able
to accurately place (or spot) cargo in the hold. On container ships using ports
without special container handling facilities, cranes with special container
handling gear are essential.
......
- Mechanically operated steel hatch covers
Hatch cover equipment like the other deck machinery, has to exist in a very
hostile environment and the importance of regular maintenance cannot be
over-emphasized. Drive boxes and electrical enclosures should be checked
regularly for water-tightness.
......
- Derricks and cargo winches -Ship cargo handling gears
The duty of a deck winch is to lift and lower a load by means of a fixed rope on
a barrel, or by means of whipping the load on the warp ends, to top or luff the
derricks, and to warp the ship.
......
Home page||Cooling ||Machinery||Services ||Valves ||Pumps ||Auxiliary Power ||Propeller shaft ||Steering gears ||Ship stabilizers||Refrigeration||Air conditioning ||Deck machinery||Fire protection||Ship design
||Home ||
General Cargo Ship.com provide information on cargo ships various machinery systems -handling procedures, on board safety measures and some basic knowledge of cargo ships that might be useful for people working on board and those who working in the terminal. For any remarks please
Contact us
Copyright © 2010-2016 General Cargo Ship.com All rights reserved.
Terms and conditions of use
Read our privacy policy|| Home page||