Home page||Machinery service system||
Air compressors working principles- Machinery service systems and equipment for motorships
Two stage starting air compressor
The compressor illustrated in Figure 1 below is a Hamworthy 2TM6 type which was designed for free air deliveries ranging from 183 m3 per hour at a discharge pressure of 14 bar to 367m3 per hour at 42 bar. The crankcase is a rigid casting which supports a spheroidal graphite cast iron crankshaft in three bearings.
The crankshaft has integral balance weights and carries two identical forged steel connecting rods. Both the first and second stage pistons are of aluminium alloy with cast iron compression rings. Scraper or oil control rings are fitted to return to the crankcase, most of the oil being splashed on to the cylinder walls from the bottom ends.
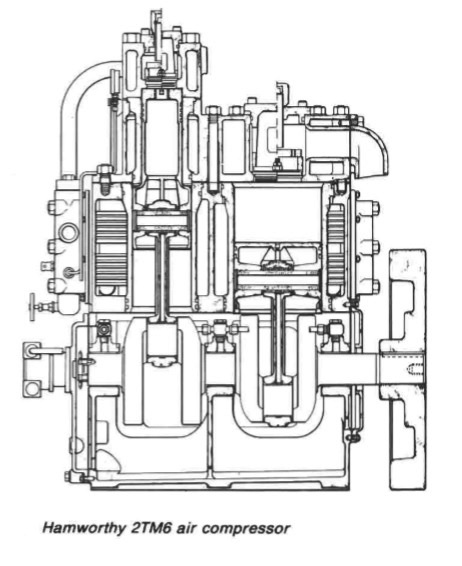
Figure 1: Hamworthy 2TM6 air compressor
The cylinder walls are lubricated by the splashed oil The pistons have fully floating gudgeon pins; connecting rod top ends house phosphor bronze bushes. The bushes are an interference fit in the connecting rods and are so toleranced that the collapse of the bore when fitting is allowed for, to provide the correct running clearance. Steel backed white metal lined 'thin shell' main and crankpin bearings are used and all of the bearings are pressure lubricated by a chain driven gear pump. Air suction and discharge valves are located in pockets in the cylinder heads.
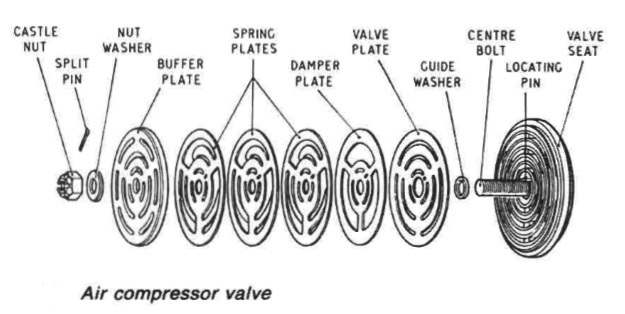
Figure 2 : Air compressor valve
The valves are of the Hoerbiger type and are as shown in Figure 2 above. The moving discs of the valves have low inertia to permit rapid action. Ground landings are provided in the pockets on which the valve bodies seat. The bodies are held in place by set screws which pass through the valve box covers, capped nuts being fitted to the ends of the set screws.
A combined air filter and silencer is fitted to the compressor air intake. The intercooler is of the single pass type. The shell forms an integral part of the cylinder block casting, with the air passing through the tubes. The aftercooler is of the double pass U-tube type. Again the shell is integral with the cylinder block.
Relief valves are fitted to the air outlets of each stage and are set to lift at 10% above normal stage pressure. The actual stage pressures vary according to the application. To protect the water side against over pressure in the event of a cooler tube failure, a spring loaded relief valve or bursting diaphragm, is fitted on the cylinder jacket. Protection against overheating in the compressor discharge, is afforded by a fusible plug fitted on the aftercooler discharge head. Overheating sufficient to melt the alloy material of the plug can be the result of carbon build up around the discharge valve.
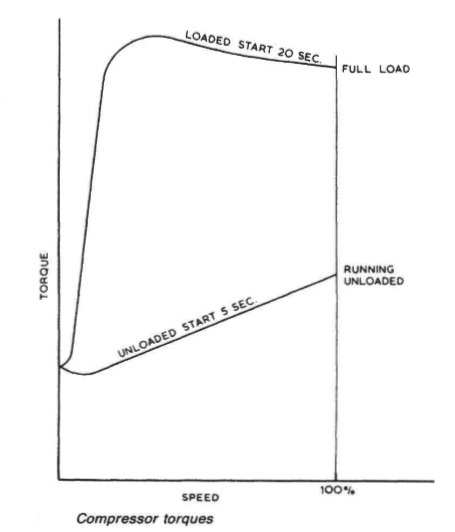
Figure 3: Air Compressor torques
Operation and maintenance
Compressors must always be started in the unloaded condition otherwise pressures build up rapidly producing very high starting torques (Figure 3 above). During running there is an accumulation of oil carried over from the cylinders and water from moisture, precipitated in the coolers. The emulsion is collected in separators at cooler outlets and these must be drained off regularly, to reduce carry over. This is extremely important, first to prevent any large quantity of water and oil emulsion reaching a subsequent compression stage and causing damage to a further stage and secondly to reduce the amount carried over to the air receivers and starting air lines.
Moisture in air receivers can give rise to corrosion and despite the proper operation of compressor cooler drains, a large amount tends to collect, particularly in humid conditions or wet engine rooms. It is good practice to check air reservoir drains regularly to assess the quantity of liquid present.
In extreme conditions, drains may have to be used daily to remove accumulated emulsion. This is very important if air for control systems is derived from the main receivers, to prevent problems with the reducing valve, moisture traps and filters. Moisture traps for the control air system also
require regular checking and possibly daily draining.
A compressor is unloaded before being stopped by opening the first and second stage drains. The maker's instructions normally recommend the use of a light oil for crankcase and cylinder lubrication. Diesel engine erankcase oils, which are likely to be a blend of light and heavy stocks, tend to produce deposits. The oil is inclined to emulsify and should be changed at frequent intervals. Excessive operation of automatically controlled compressors (usually due to a large number of leaks rather than actual use of air) usually means that valves require frequent cleaning and maintenance.
Failure to keep valves in good condition, results in valve leakage and overheating with an associated accumulation of carbon on the valves and in valve pockets. The combination of carbon, excessive temperature and the high concentration of oxygen in compressed air can result in fire or explosion in the discharge pipe. The effect of fire in a compressor discharge, has been known to weaken the pipe causing a split through which flame, supported by the compressed air, has emerged, Poor valve condition can be detected by observation of the stage pressures and is usually accompanied by excessive discharge temperature although the latter can also be a symptom of poor cooling.
Adequate attention must be given to the water cooling system. Overcooling can cause condensation on the cylinder walls, adversely affecting lubrication, while poor cooling, due probably to scale formation in a sea-water cooled machine, will result in a fall-off in volumetric efficiency and rapid valve deterioration. Inter- and after-coolers require periodic cleaning to remove scale (where they are sea-water cooled) and oily deposits from the air side. With respect to temperature limitation, classification societies require that the compressor should be so designed that the air discharge to the reservoir should not substantially exceed 93 deg C.
Summarized below some of the basic procedure of machinery service systems and equipment :
- Marine air compressor
A single stage compressor used to provide air at the high pressures required for diesel engine starting, would unfortunately generate compression temperatures of a level similar to those in a diesel. Such heat would be sufficient to ignite vaporized oil in the same way as in a compression-ignition engine. The heat produced in a single stage of compression would also be wasteful of energy.....
- Air starting system
Air at a pressure of 20 to 30 bar is required for starting main and auxiliary diesel engines in motorships and for the auxiliary diesels of steamships. Control air at a lower pressure is required for ships of both categories and whether derived from high pressure compressors through reducing valves or from special control air compressors, it must be clean, dry and oil free.....
- automatic-operation-air-compressor
Before the general introduction of control equipment, air compressors were stopped and started by engine room staff, as necessary, to maintain air receiver pressure. In port or at sea, this usually meant operating one compressor for about half an hour daily unless air was being used for the whistle (during fog), for work on deck or for other purposes. ....
- Compressed air systems for steamships
A compressed air system is necessary to supply air for boiler soot-blower air motors, hose connections throughout the ship and possibly diesel generator starting. A general service air compressor would supply air at 8 bar but greater pressure (as for diesel ships) would be necessary for diesel starting.....
- Two stage starting air compressor
Hamworthy 2TM6 type which was designed for free air deliveries ranging from 183 m3 per hour at a discharge pressure of 14 bar to 367m3 per hour at 42 bar. The crankcase is a rigid casting which supports a spheroidal graphite cast iron crankshaft in three bearings.....
- Fuel handling
Fuels and lubricating oils are obtained from crude primarily by heating the crude oil, so that vapours are boiled off and then condensed at different temperatures. The constituents or fractions are collected separately in a
distillation process.....
- Fuel transfer and fire risk
The oil fuel system provides the means for delivering fuel from the receiving stations at upper deck level, port and starboard, to double-bottom or deep bunker tanks. Sampling cocks are fitted at the deck connections to obtain a representative specimen for (a) shore analysis; (b) on board testing; and (c) retention on the ship.....
- High density fuel treatment
The density of a fuel tested at 15 deg C may approach, be equal to or greater than that of water. With high density fuels, the reduction in density differential between fuel and water can cause a problem with separation but not with the usual solid impurities.....
- Viscosity controller
A continuous sample of the fuel is pumped at a constant rate through a fine capillary tube. As the flow through the tube is laminar, pressure drop across the tube is proportional to viscosity. In this unit an electric motor drives the gear pump through a reduction gear, at a speed of 40 rpm......
- Fuel blenders
Conventionally, the lower cost residual fuels are used for large slow speed diesel main engines and generators are operated on the lighter more expensive distillate fuel. The addition of a small amount of diesel oil to heavy fuel considerably reduces its viscosity and if heating is used to further bring the viscosity down then the blend can be used in generators with resultant savings.....
- Fuel heaters
The system which delivers residual fuel from the daily service tank to the diesel or boiler, must bring it to the correct viscosity by heating.For burning heavy fuel oil in a boiler furnace, or a compression-ignition engine, it is necessary to pre-heat it....
- Homogenizer
The homogenizer provides an alternative solution to the problem of water in high density fuels. It can be used to emulsify a small percentage for injection into the engine with the fuel. This is in contradiction to the normal aim of removing all water, which in the free state, can cause gassing of fuel pumps, corrosion and other problems......
- Package boiler combustion system
The elementary automatic combustion system based on a two flame burner is used for many auxiliary boilers. The burner is drawn oversize to show detail. Various different control systems are employed for the arrangement.....
- Lubricating oil treatment
Mineral oils for lubrication are, like fuel, derived from crude during refinery processes. Basic stocks are blended to make lubricants with the desired properties and correct viscosity for particular duties. ....
Home page||Cooling ||Machinery||Services ||Valves ||Pumps ||Auxiliary Power ||Propeller shaft ||Steering gears ||Ship stabilizers||Refrigeration||Air conditioning ||Deck machinery||Fire protection||Ship design
||Home ||
General Cargo Ship.com provide information on cargo ships various machinery systems -handling procedures, on board safety measures and some basic knowledge of cargo ships that might be useful for people working on board and those who working in the terminal. For any remarks please
Contact us
Copyright © 2010-2016 General Cargo Ship.com All rights reserved.
Terms and conditions of use
Read our privacy policy|| Home page||